The starting
point - the mirror on its face on the left, and the old solid
double plywood mirror cell mount for the square tube. It is coated
with gray epoxy on the top.
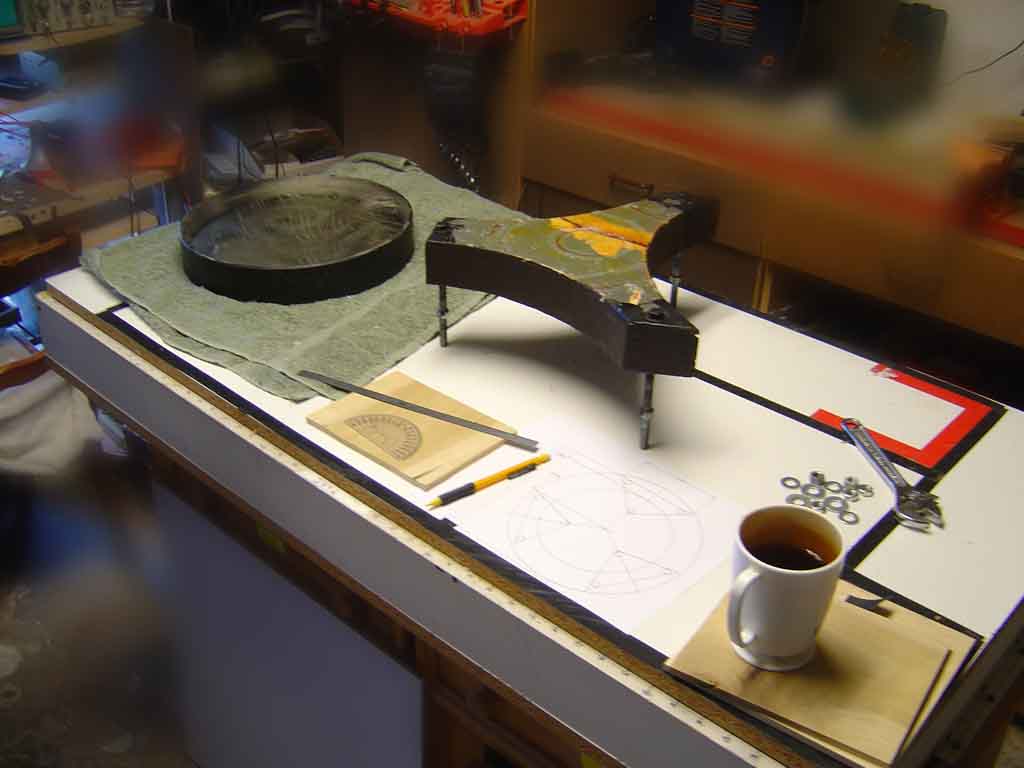
The layout was
drawn up in Autocad to get the sizes of the support triangles
and the placement around the 70% zone.
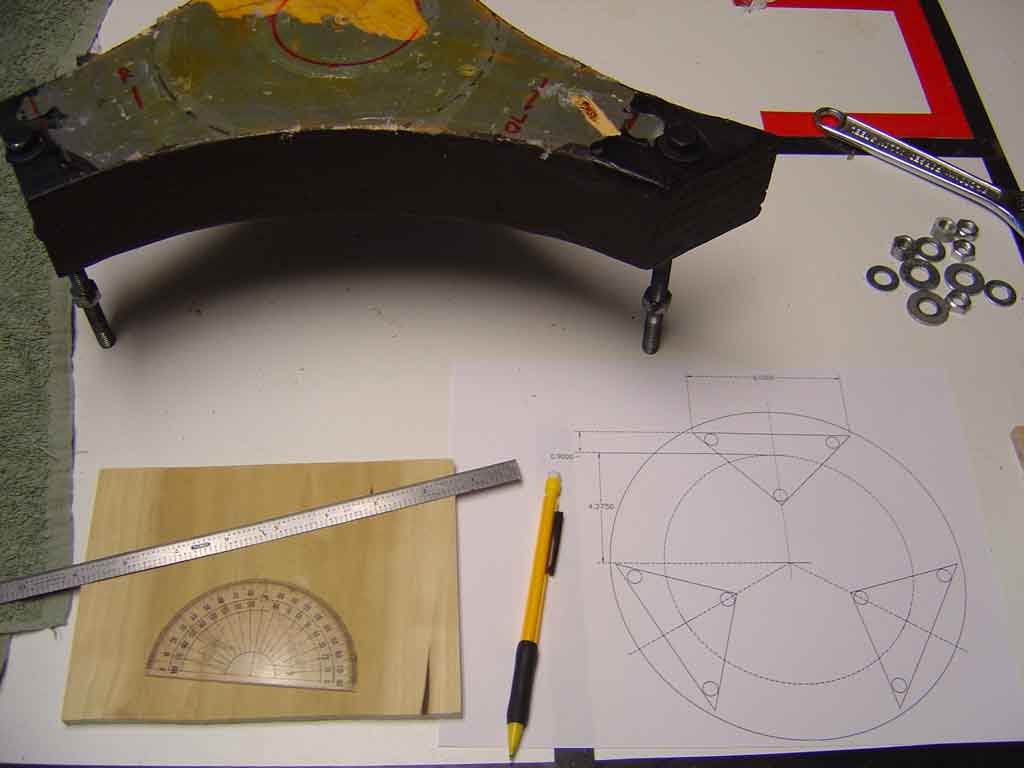
First I glued in
with epoxy three stainless steel acorn nuts at the mounting point
for the support triangles. They stick up out of the counter bore
around 3/16".
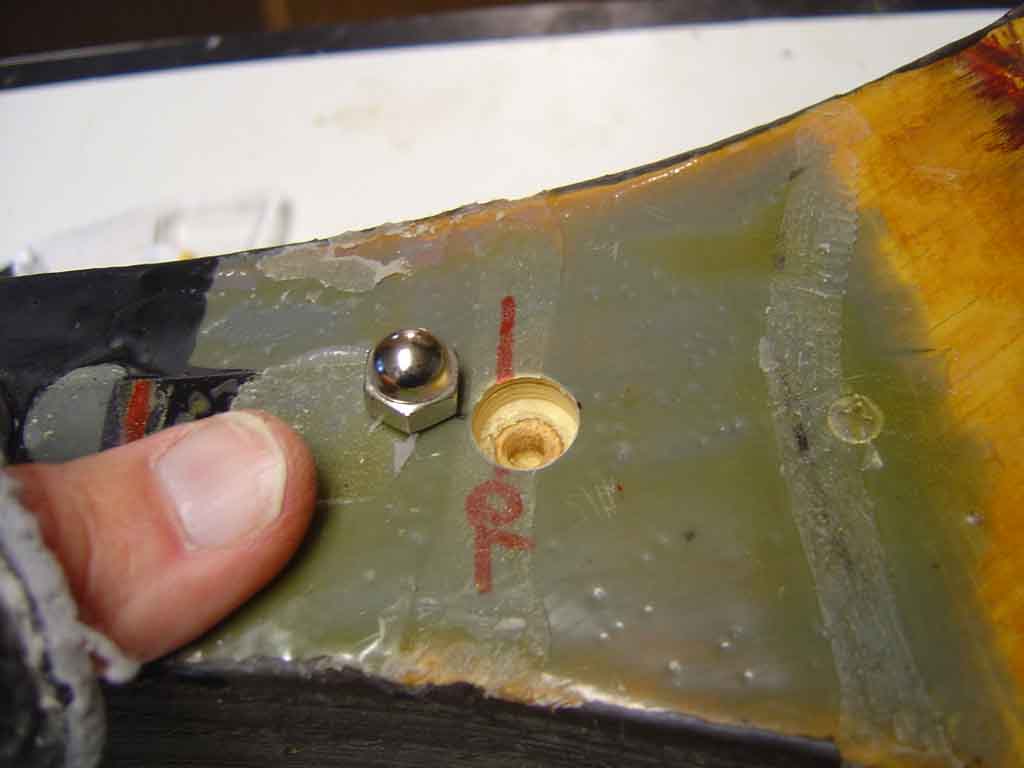
Cemented in place,
the acorn nut is the tilt bearing for the triangles.
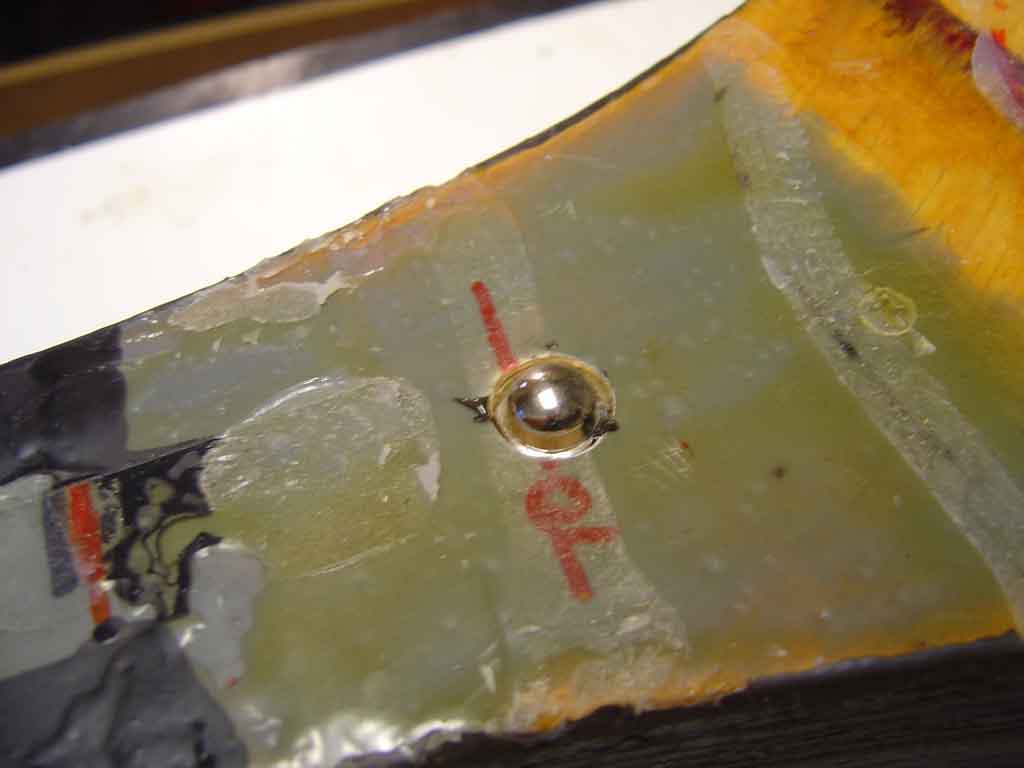
The triangles consist
of three pieces about six inches long across the hypotenuse on
1/4" solid ash hardwood. Each bottom has a countersink with
a steel washer to match up with the acorn nut for a tilt surface.
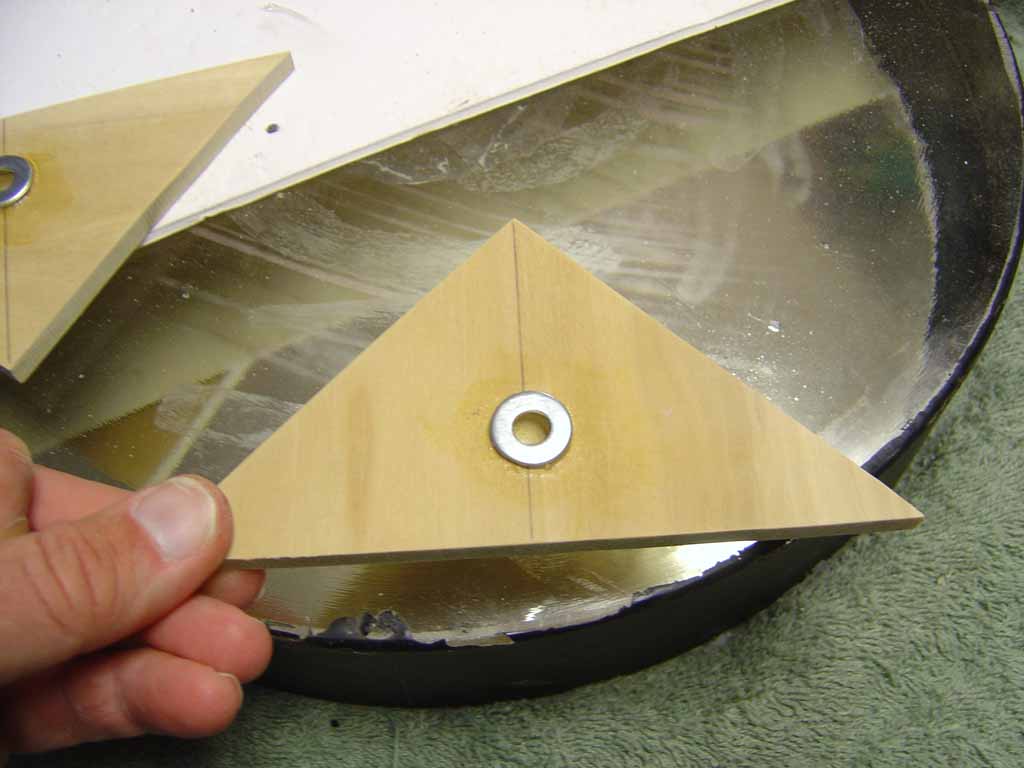
Gluing the cork
pads onto the triangles.
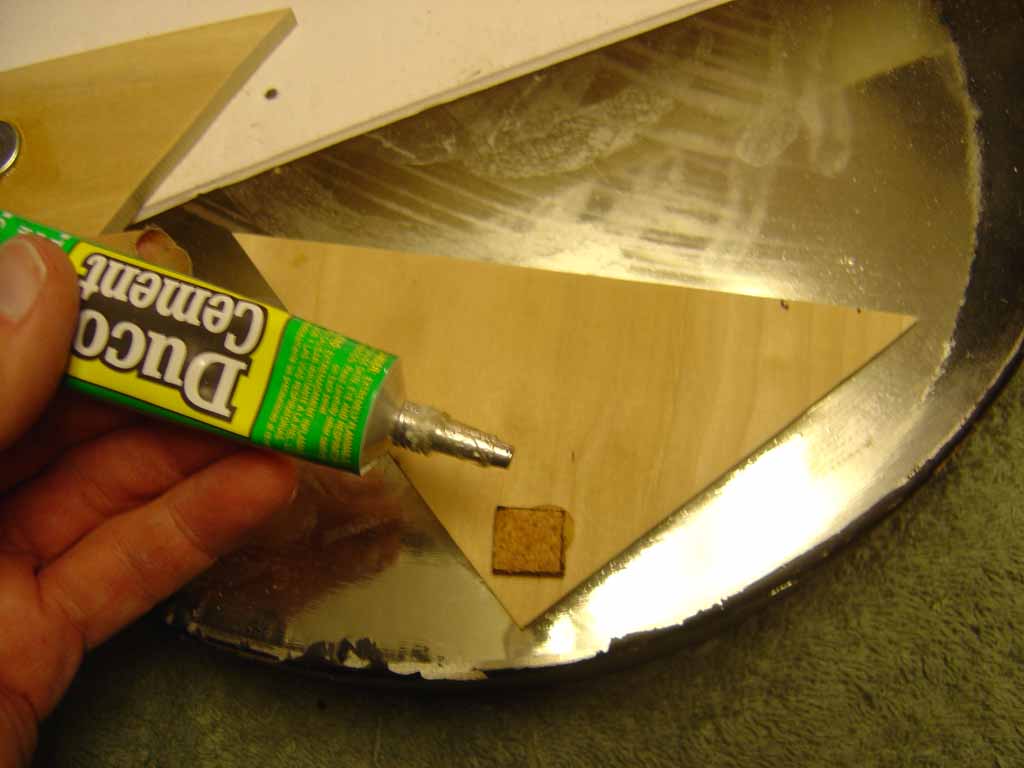
Three support triangles
in place on the acorn nuts, with 9 pads for support on the back
of the mirror. They each tilt a bit to conform to the back of
the mirror. This is what is meant by a "Floatation Support"
system.
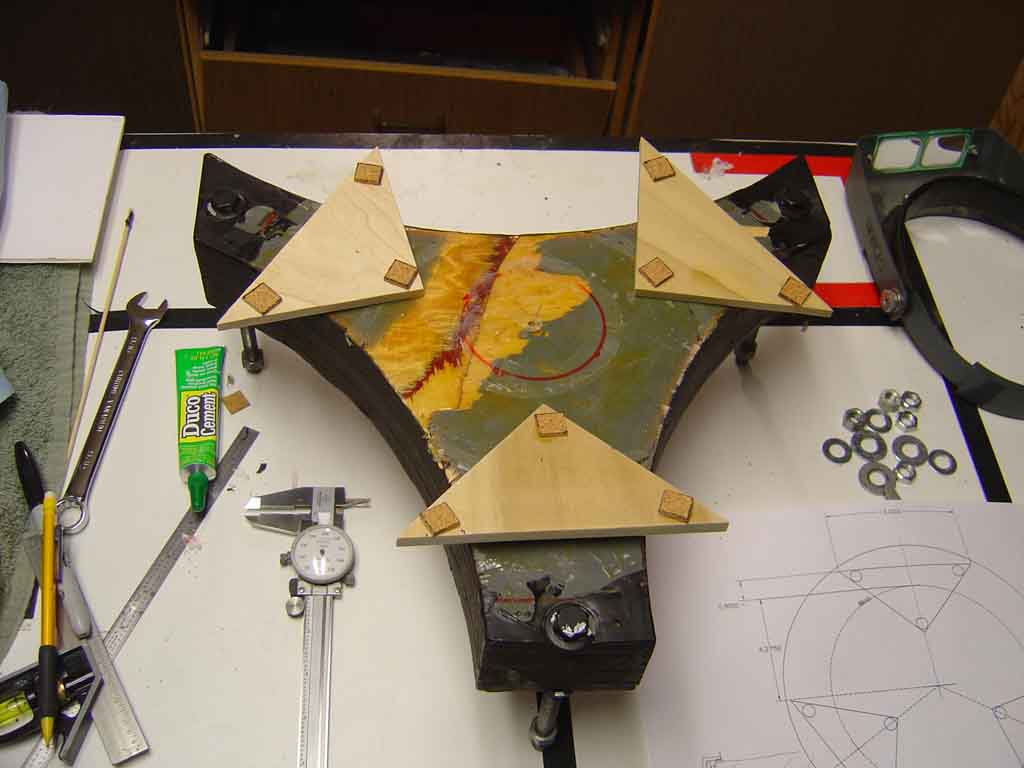
Under the side
of the mirror sitting on the cell, you can see the cork pads
are supporting the mirror nicely and the are then held up about
1/8" from the mirror cell base by the acorn nut bearings.
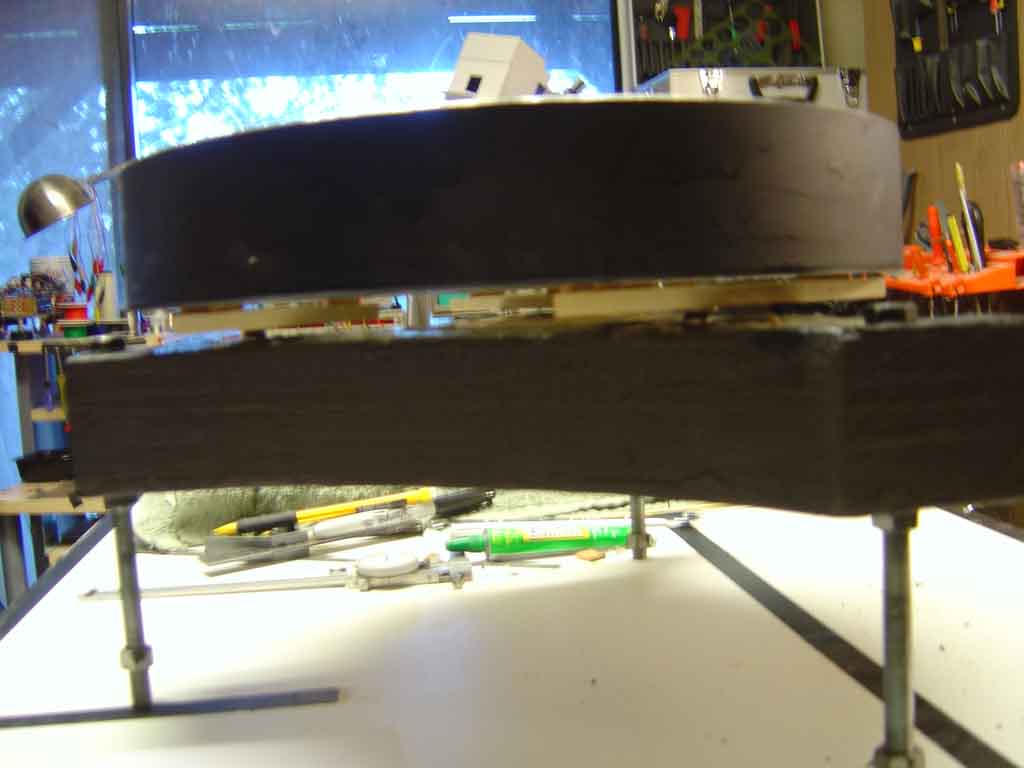
Gluing the cork
pads on the side brackets and mirror clips!
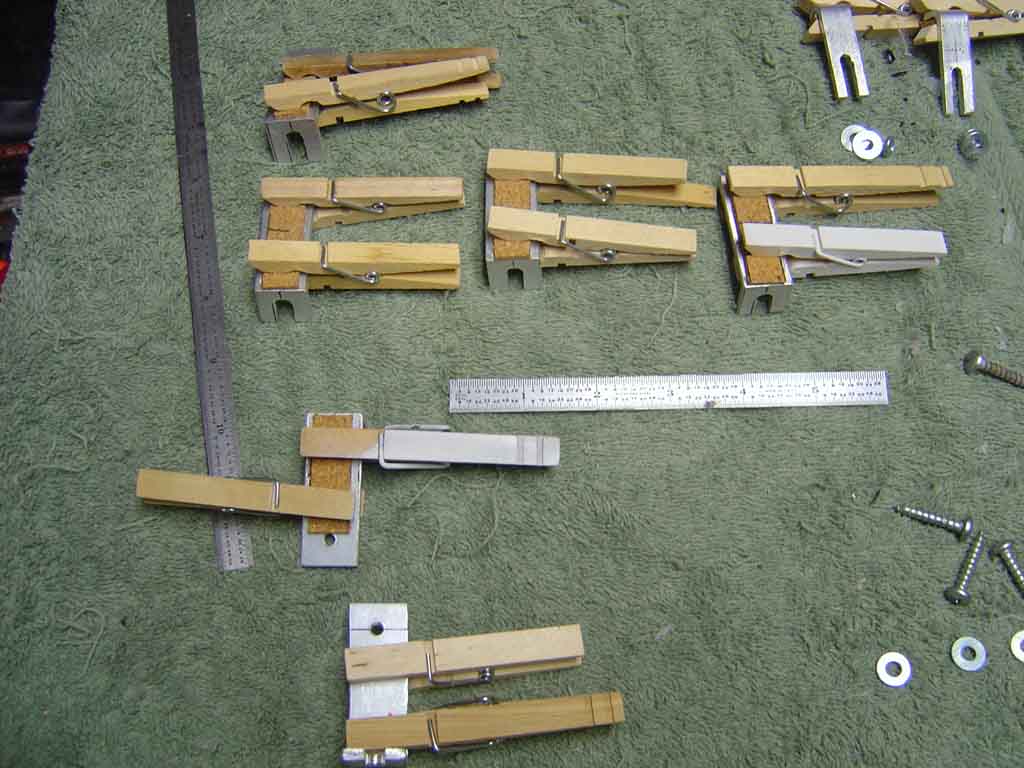
Before painting,
here I assembled the clips. Three sets are made, to support the
sides of the mirror and hold it in place.
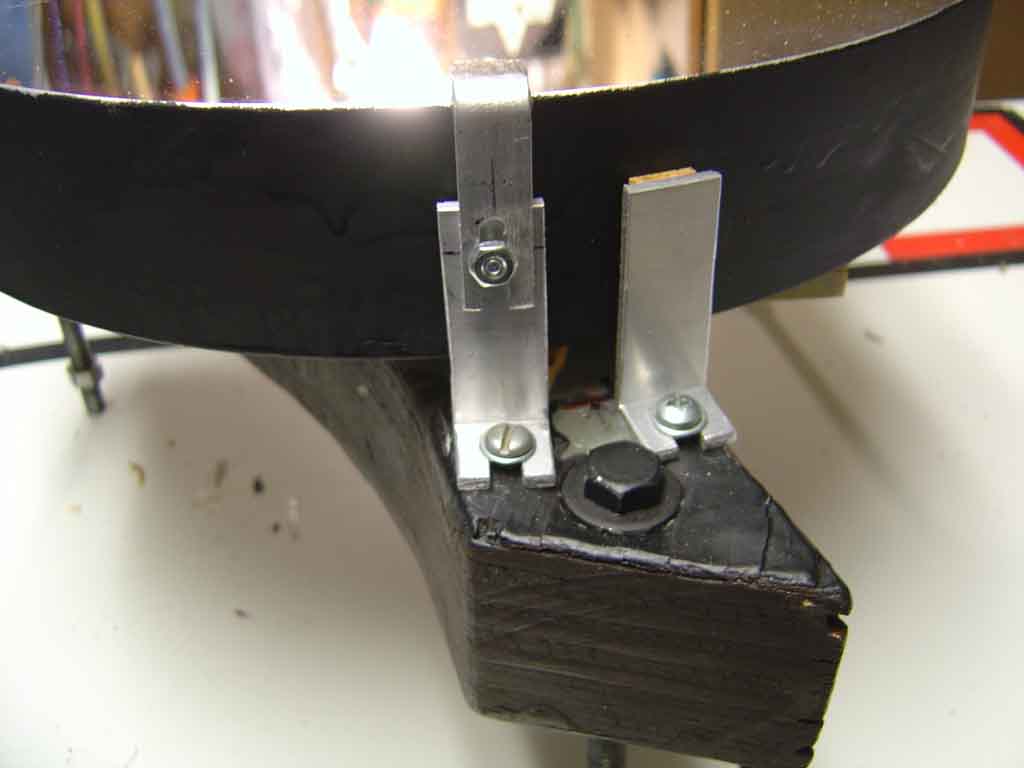
Getting ready to
paint, the cork is masked off with tape and ready to shoot! The
screw heads and washers too are masked by pushing them into Styrofoam.
This keeps the threads clean.
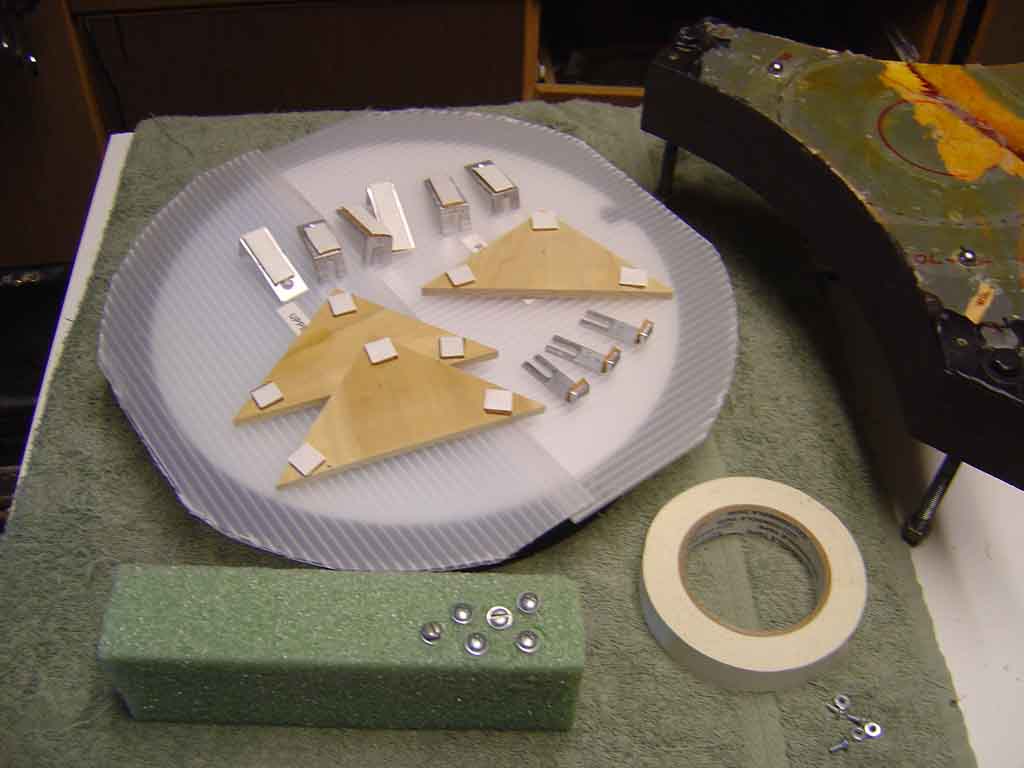
The painted components
installed - the base board has been sprayed flat black as well.
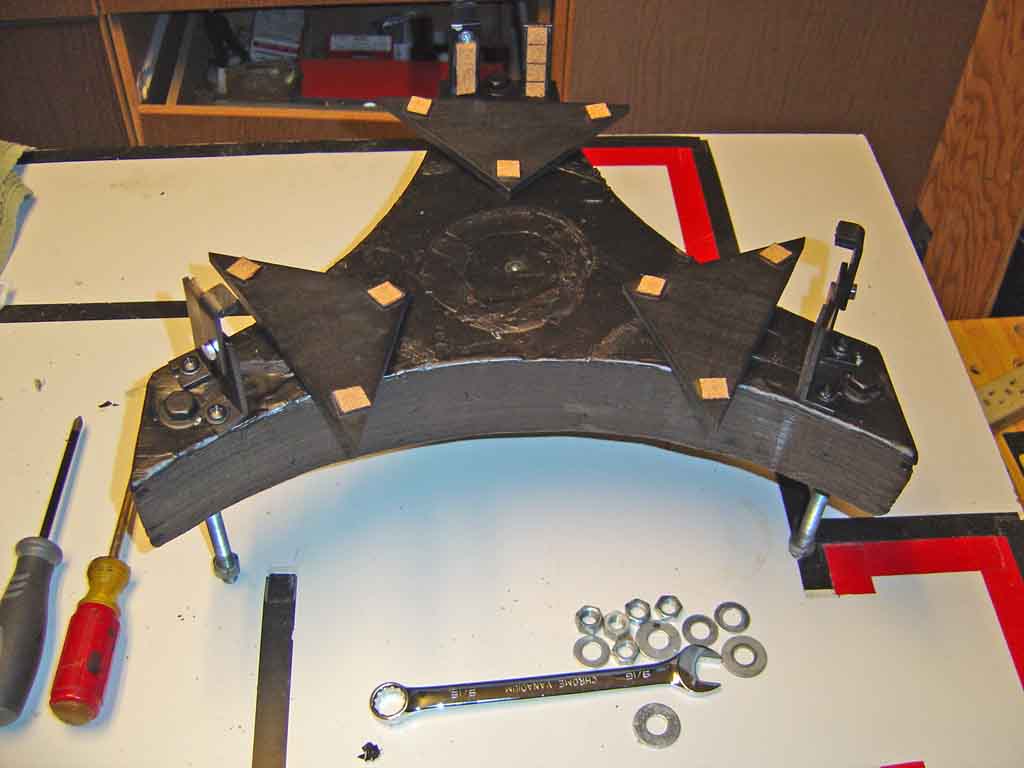
Finally, the mirror
is installed and the side pieces are carefully seated as to not
stress the mirror. The top clips are shimmed so they are about
.015" over the surface.
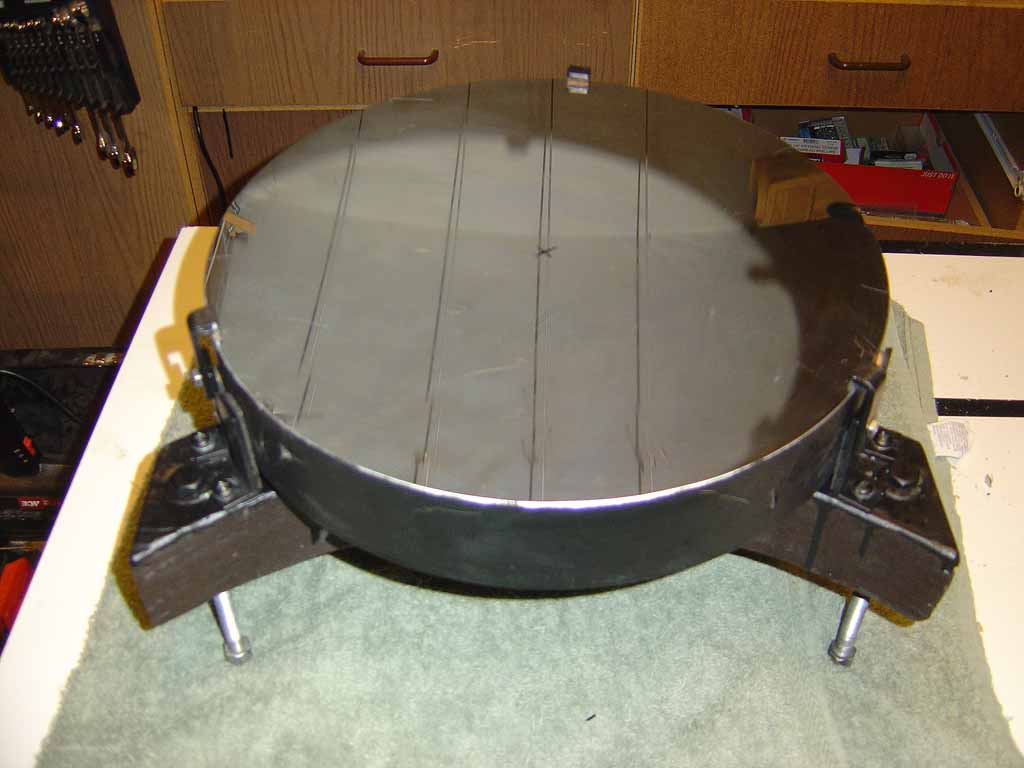
Final star testing
will be next, I have no doubt that the system will far outperform
the old glue mount I had before!
|