Introduction:
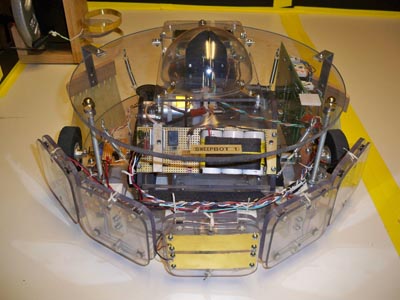 |
This
new robot is a second round on the engineering of a simplified
floor cleaning drone, the first was Vacbot completed a few years
back. Unlike that robot, which was built from a modified commercial
floor sweeper, SweepBot is completely custom built from the ground
up. The task of this new robot is simple: Perform a daily short
period clean sweep of the bathroom tile floor, to keep litter
that has escaped from the cats litter box at bay. The robot must
be autonomous, with little maintenance other than an occasional
emptying the dust bin from an operator. |
Mode of Operation:
The robot consists
of two separate sections, the “Carrier Robot” and the
“Mechanical Sweeper” assemblies. By separating the
two this allows simplified sweep section maintenance, or replacement
if needed. The sweeper section is nested inside the carrier,
and floats on the tile surface held up by a spring suspension.
The carrier and sweeper each have their own rechargeable batteries
connected to one charging board.
The Carrier Robot:
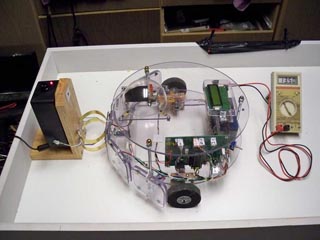 |
The
Sweepbot carrier robot is almost completely finished. Here, the
robot is connected to its IR Beacon/Battery Charger hoops which
was developed in the PICbot series of projects. The robot can
see the beacon on the charger from about 3 to 4 feet away (this
is adjustable) and will drive to the charger when done sweeping
for the day. The charger contacts contains 15vdc at 1 amp and
a small charging board on the robot limits the charging on the
gel cell. |
This is where the
primary movement and intelligence is located. The base consists
of a two deck lexan construction, driven by two dc motors under
the base level.Also on the base level is the 12v gel cell battery,
microcontroller PCB, and touch sensors (bumpers). The top deck
carries the LCD display and the IR docking fine guidance sensor
bubble. The robots primary circuit board is our first home designed
printed circuit board, and is designed to be a universal robot
board as well complete with motor drivers and sub processors.
Sweeper Section:
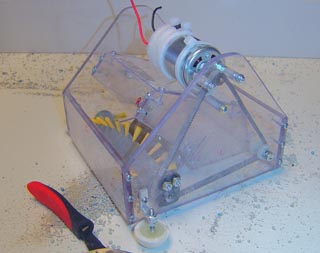 |
I
actually built this section first, because I wasn’t sure
how big it was going to be to do the job. Also constructed of
heavy lexan, this motorized brush section has a small dust tray
that can be dumped by releasing a magnetic door. A small circuit
board on the side carries both the 4v NMh batteries for independently
running the motor, and a buffered relay for simplified on/off
operation with the microcontroller on the main robot. Since I
am running the motor at half the voltage, it is relatively quiet
and needs a smaller battery pack. It will run up to 30 minutes
on an overnight charge if needed. |
The Docking Station:
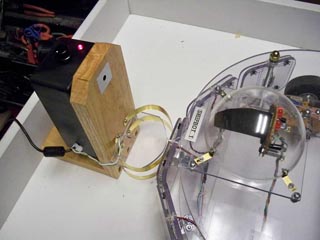 |
The
docking technology in this base was used from the best performing
design on the Picbot 5 project – “Docking Logic”.
Two brass hoops with a lexan separator are connected to a 15v
1A commercial power supply plugged into the wall outlet. This
will trickle charge the batteries when the robot is docked. The
power supply also operates the internal circuit board which consists
of a 38.5 KHz oscillator connected to the IR beacon LED. This
projects a narrow beam over three feet to allow the robot to
home in on the charging base. |
New Technologies
While the artificial
intelligence of this robot was heavily based on the techniques
developed in the PICbot series, several new technologies were
used for the first time on SweepBot. Here is a list detailing
these developments:
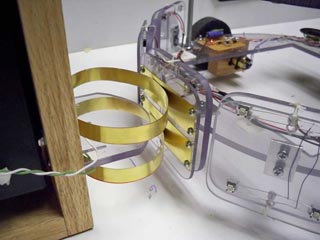 |
-
New impact bumper design – Using four touch contact type
micro switches sandwiched between two lexan plates was a new
and very reliable concept that was plenty sensitive and had great
flexibility in the morphology. |
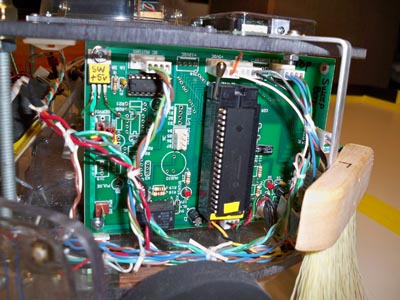 |
-
New universal robot PCB – For the first time, a PCB was
designed in Express PCB design software, and several boards were
made. The board is intended to be universal, containing a large
16F874a processor several Texas instruments motor driver chips,
and two additional slave PIC 8 pin processors for servo control.
About half the board was filled here, only what was used in this
design. |
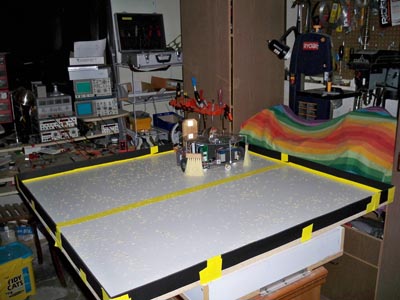 |
-
New larger robot test arena – The 14 inch size of Sweepbot
made it essential that the testing arena had to be larger. Two
white fiber board sheets combine to make a 48 inch square arena,
with three inch sides all around. In the future, this larger
size will make working with smaller robots seem like a whole
new huge universe! |
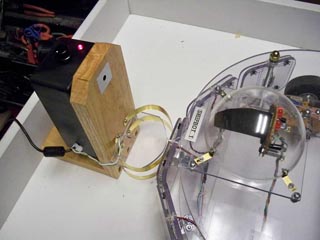 |
-
New docking contact design – The dual hoop design used here
was developed in the PICbot 5 project to be the most flexible
and reliable contact arrangement for robot docking and charging.
The contacts can compress about a half an inch to accommodate
the incoming robot which has dual plates mounted on the center
bumper to mate up with the hoops. It works very well in this
larger robot and Is fully scalable for future bots as well. |
System Operation:
The robot is programmed
with PIC Basic to run a “Finite State Machine” (FSM)
type of program, which provides the framework for the artificial
intelligence of the system. There are many caveats and error
conditions that can occur in a robot that is designed for full
time 24 hour a day operation! It took me the better part of six
months to craft the software to run the robot autonomously. The
basic operation of the Sweepbot is to awaken on the charger at
the first light of day. Next, after it confirms the sun is really
rising, and its getting brighter for a half hour or so, it undocks
from the charging base, and starts the sweep mode. The robot
moves about the room, using the bumpers to avoid walls and obstacles.
The AI for this was fully developed in the PICbot I program.
The power is applied to the sweeper at this time. After running
for about 10 minutes, the robot starts looking for its charger
and turns off the sweeper. When it finds the charger, it docks
with the charger which is located in a tight space between the
bathtub and toilet. It then confirms the presence of a charging
voltage, then shuts down and waits the rest of the day for the
onset of night. Once night is found when its getting dark after
sunset, it changes modes and searches again for the sunrise.
Then it will live its life again, over and over, day after day
keeping the floor cleared of bits of cat litter.
Testing and Evaluation:
Months of extensive
testing lasting sometimes for weeks on end were performed on
this robot while it was in four foot square “robot arena”.
There, every condition conceivable that it might encounter in
real life was simulated and programmed for. Uncooked rice was
used for faux cat litter for simplified testing of cleaning action,
and the development of the docking, and charging systems. Once
the robot performed a given period of time with any new changes,
we would move on to the next phase. Then there would be few surprises
when the robot was moved to its final cleaning destination upstairs.
Final Summary
This will be a
long term on going project. While I don’t see too many issues
with the carrier robot, how long the sweeper section will hold
up remains to be seen. Because it is modular, replacing the sweep
section with a new design is relatively straight forward. In
six months, Ill post an update here – stay tuned!
Photo Gallery
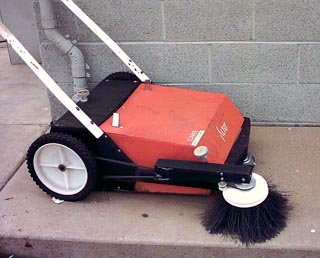 | My
inspriration, when I started this project 1 year & 4 months
ago, I saw this parking lot sweeper behind the circle K in town.
It works by pushing it and the back wheels drive the brush to
push the trash FORWARDS into the catch bin via a rubber ramp.
The rear wheel also drives a side brush to sweep stuff in the
curbs in front of the sweeper intake. The robots side brushes
do this very same task. |
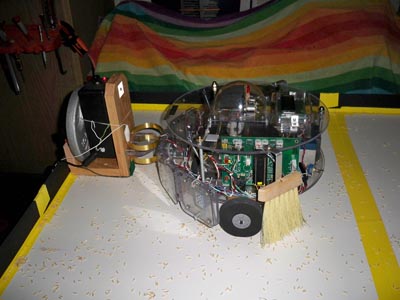 | Docked
on a rice sweeping test run. The side brushes can be seen well
here, and were cut with a bandsaw from a plasterers spreading
brush. It is one row of six that were on the brush. |
 | Bottom
sweeper side view. The rotating brush pushes the dirt forward
up the polycarbonate ramp into the catch bin. Note the three
white round slides the sweeper runs on. |
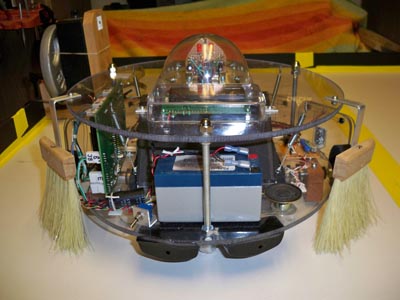 | Rear
veiw showing the battery and position of the side brushes. |
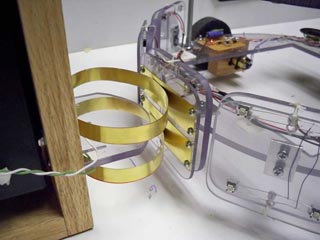 | The
robots front bumper has two brass plates for connecting to the
charger. The robot drives up to the flexible hoops, connects
by confirming the presence of a voltage, then stops to charge.
The hoops can be docked with from a wide variety of angles. |
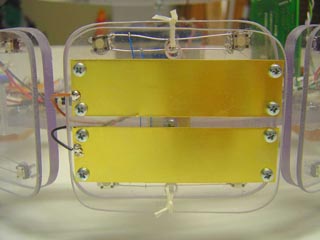 | Here
is the front central bumper of the robot showing the two brass
plates for charging. |
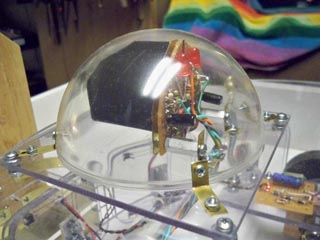 | The
robot homes in on the IR beacon on the charging base with this
vane type two sensor detector, which contains two PN4602 IR prox
sensors. Ive enclosed it in a plastic bubble to protect it. |
|